FLEXIBLE POLYURETHANE PLANT
The OPTIFOAM V7 is a Slabstock Continuous Flexible Polyurethane Foaming Plant designed to produce consistent quality of highly regular, flat topped foam blocks.
It operates on Low Pressure Downward Foaming Principle.The individual chemicals from the tanks are metered in to high speed Mixing head by accurate Positive displacement pumps, which are controlled by microprocessor drives.

OPTIFOAM V7 has seven chemical streams – Polyol, TDI, Silicon, Amine, Stannous Octoate, Water and Methylene Chloride. Additional lines for pigment and additives dosing can be incorporated optionally. The mixture is led from the Mixing Head into a Foaming trough through a pair of flexible hoses. A diaphragm Valve located at the outlet of the Mixing Head enables accurate control of the mixing head pressure and thus the cell structure of the resultant foam. The chemical mixture spills over the edge of the trough onto the first of a series of metallic fall plates. The number of the fall plates may be 4 or 5 depending upon the machine. The slope of the fall plates is adjustable from the control panel. Almost 70% of rising takes place over the Fall Plates and the rest over the horizontal, metal slat conveyor. The regular and uniformly flat topped foam train reaches the end of the foaming tunnel over the conveyor, where it is cut off by a block cutter to obtain regular rectangular shaped foam blocks. The width of the Foaming Tunnel is variable between 1.4 mts. to 2.1 mts. and can be set by a powered system from the operating platform.


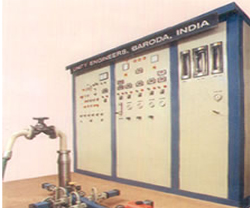
✢ Flat Topped Regular Foam Blocks with minimum wastage/scrap.
✢ Greater block heights compared to conventional machines.
✢ Better ILD values.
✢ Hassle-free and easy to operate plant with low manpower cost.
✢ Low specific power consumption, hence economical in operation.
✢ Flexibility of foaming width due to variable Foaming Tunnel width.
✢ Reliable and customer-friendly service backup.
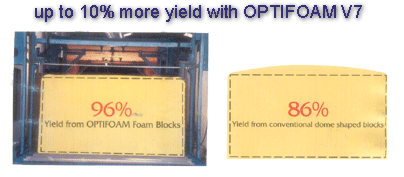